Simutence is your highly specialized and independent partner for virtual design with plastics, fiber-reinforced composites, and hybrids. Using advanced engineering and simulation approaches, we are here to make product design and manufacturing time- and cost-efficient.

Generate a digital twin of
manufacturing processes and products
Leverage from advanced engineering and simulation methods
Enable material and manufacturing efficiency
Benefit from our international
network and partners

Our approach to the efficient development of manufacturing processes and components is the seamless and close connection of product design, manufacturing validation, and engineering through our virtual process chain. Based on this, virtual manufacturing validation is enabled, which can significantly reduce real-world efforts on demonstrator manufacturing and manufacturing piloting.
Selected customers
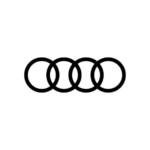
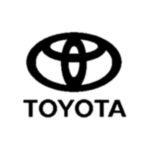
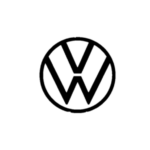
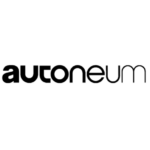
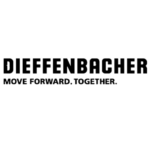
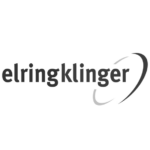
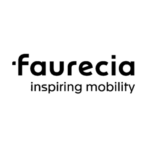
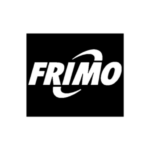
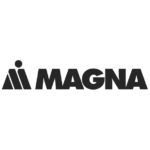
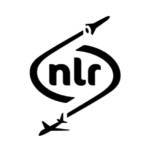
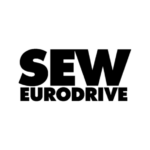
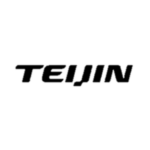
Virtual Process Chain
»Seamlessly connect product design, manufacturing validation, and engineering using Simutence approaches to generate a virtual process chain.«
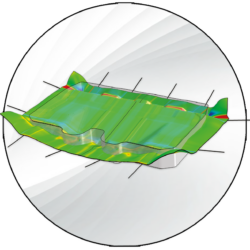
Forming Simulation
- Validation of manufacturability
- Optimization of gripper, clamping, and sequential forming setups
- Support of mold design
- Prediction of local fiber orientation and fiber volume content
- Thermomechanical-thermokinetical analysis for thermoforming
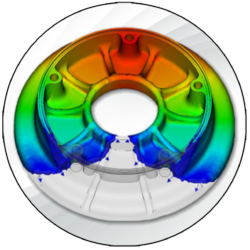
Mold Filling Simulation
- Material card creation
- Validation of manufacturability
- Prediction of filling behavior, required press forces, and suitable processing temperatures
- Prediction of the pre-forming of complex initial charge configurations
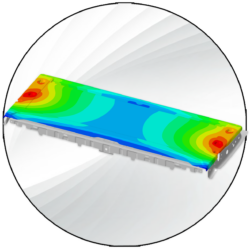
Warpage simulation
- Validation of dimensional stability
- Prediction of process-induced deformations (warpage, spring-in)
- Prediction of solidification and residual stresses
- Prediction of crystallization (thermoplastics), and curing (thermosets)
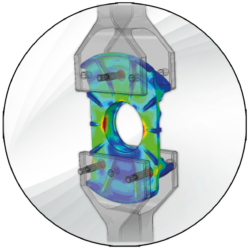
Structural Simulation (FEA)
- Validation of load requirements
- Consideration of manufacturing effects (e.g. local fiber orientation)
- Prediction of component stiffness and failure
- Prediction of local stresses after assembly of the actual geometry predicted by warpage simulation
Software Add-Ons & Hub
We develop software products to enable the virtual design of manufacturing processes and components with fiber-reinforced composites, plastics, and hybrids. Through our collaboration with the Karlsruhe Institute of Technology (KIT), we are able to supply modeling approaches beyond the state-of-the-art.
Simutence Hub
Our Simutence Hub is our web platform and provides access to our software. This includes the deployment of our add-ons as well as web applications. Request an account to get access and a free trial license.
Software Add-ons & Engineering Service
Our add-ons rely on Abaqus and Moldflow and extend the capabilities using the API. Moreover, we provide plugins for the fully automatized model setup. Use your existing software architecture for advanced composite simulation.
SimuFill
Kinetics and rheological models for SMC, LFT and GMT as well as thermoset injection molding.
Available through engineering services
SimuWarp
Prediction of process-induced deformations for thermoplastics and thermosets through Abaqus.
Thermoplastic: Available
Thermoset: Available through engineering services
Ways of collaboration
»We offer tailored collaboration approaches through training and consulting, independent engineering services, as well as advanced simulation approaches based on add-ons for established simulation software.«
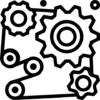
Engineering services
- Product design for fiber-reinforced composites and plastics
- Process simulation to optimize manufacturing and predict manufacturing effects
- Structural simulation (FEA) to virtually validate load requirements
- Materials characterization and material card creation for process and structural simulation
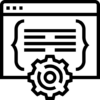
Software Add-ons
- Add-ons for enhancing the modeling capabilities of Abaqus and Moldflow
- Web applications for real-time predictions for simulation laymen as well as add-on deployment
- Customization upon request
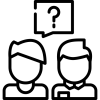
Training & consulting
- Identification and support of suitable engineering and simulation strategies
- Consulting and training on strategies for materials characterization, product design, and part manufacturing
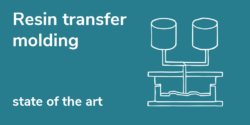
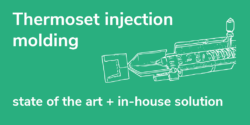
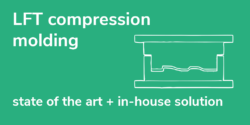
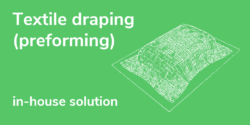
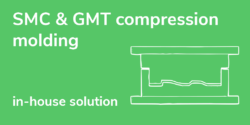
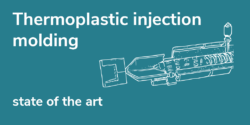
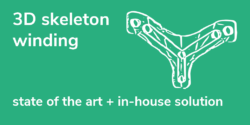
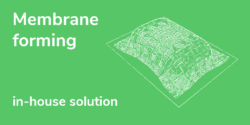
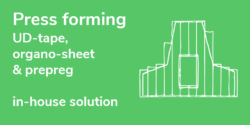
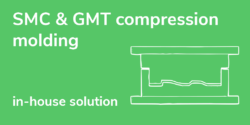
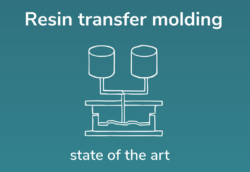
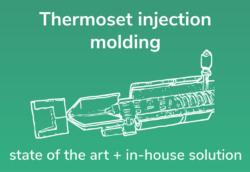
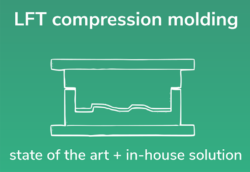
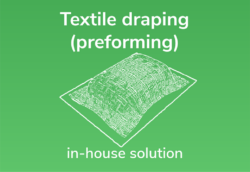
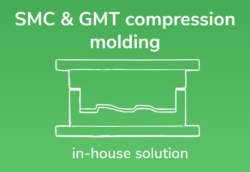
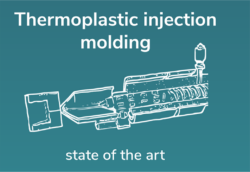
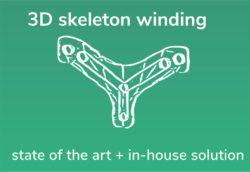
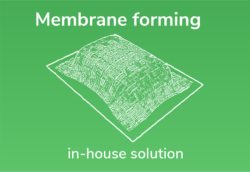
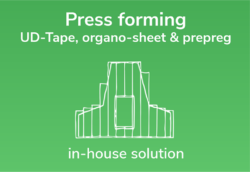

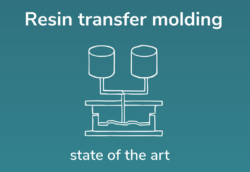
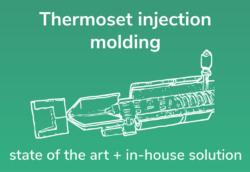
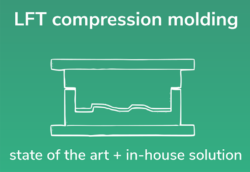
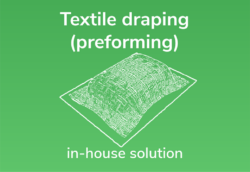
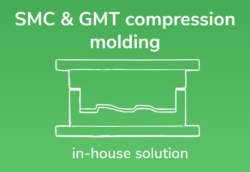
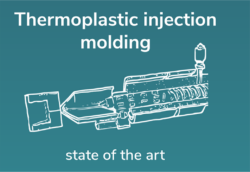
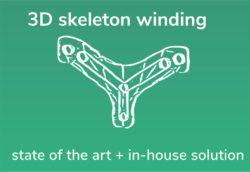
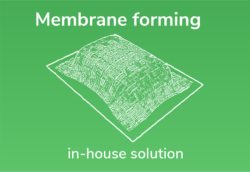
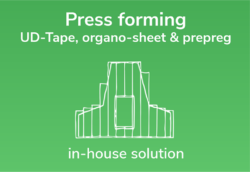

Our approach
The idea of Simutence is to use existing simulation approaches where the state-of-the-art is sufficient and to use and develop simulation approaches, where the state-of-the-art is not sufficient.
We provide our customers with access to all of our simulation approaches through engineering services. Beyond that, we successively make these approaches available to our customers, as soon as a high-quality user experience is guaranteed.
What we strive for
As a spin-off company of the Karlsruhe Institute of Technology (KIT) in Germany, we support and supply know-how and methods based on the latest state-of-the-art.
Our utmost interest is to enable you to gain maximum use from our know-how and collaboration with Simutence. Therefore, our services will be tailor-made to your specific challenge!
Seamless data stream
Our functional and modular virtual process chain is based on data transfer between the different simulation steps through mapping and homogenization approaches using our software add-on SimuChain.
Based on this, state variables such as fiber orientation or fiber volume content predicted by process simulation are retained and transferred to e.g. warpage or structural simulations.
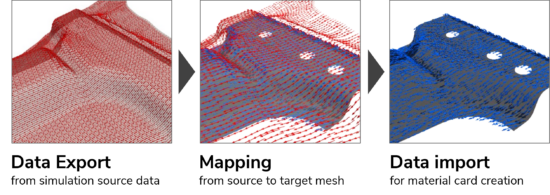
Our functional and modular virtual process chain is based on data transfer between the different simulation steps through mapping and homogenization approaches using our software add-on SimuChain.
Based on this, state variables such as fiber orientation or fiber volume content predicted by process simulation are retained and transferred to e.g. warpage or structural simulations.
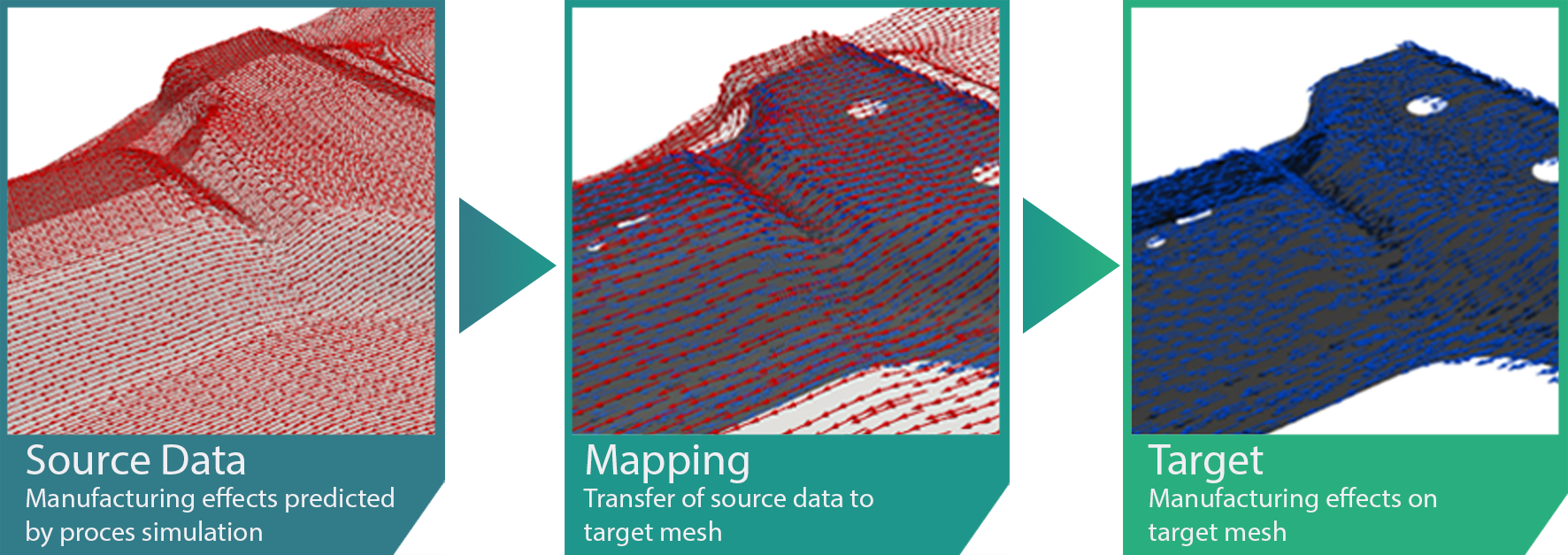
Any questions?
Do not hesitate to get in contact with us. We are pleased if you leave us a message!