Thermoforming of unidirectional fiber-reinforced thermoplastics reveals a great potential for large volume production of structural components, due to low cycle times, recyclability, and material efficiency. Therefore, thermoforming plays an increasingly important role, especially for the automotive industry.
During thermoforming, a preconsolidated blank is heated initially well above the melting temperature of thermoplastic. Subsequently, the formable blank is transferred and positioned within the mold. Finally, the mold closes and transforms the 2D blank into a 3D part. Due to cooling of the part within the mold, the thermoplastic solidifies and the part can be ejected.

Schematic of the processing steps during thermoforming.
Thermoforming processes are influenced by several processing parameters, like stacking sequence, tool temperature, initial laminate temperature, forming velocity, or laminate gripping. Depending on these parameters, as well as on the formed geometry, manufacturing defects such as local wrinkling are possible. Moreover, a modification of the fiber structure, such as a changing of fiber orientation, is inevitable.
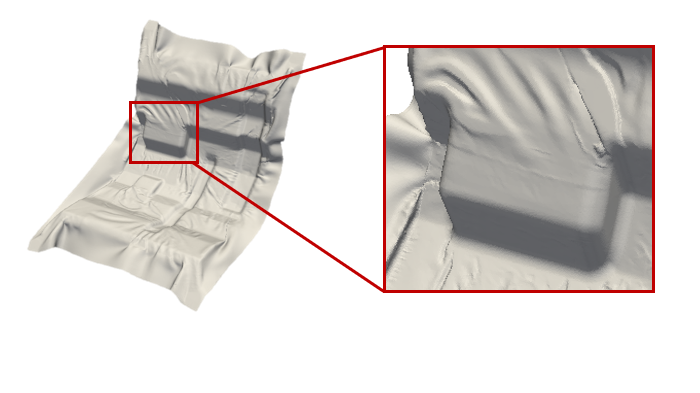
Local wrinkling for a partly formed part
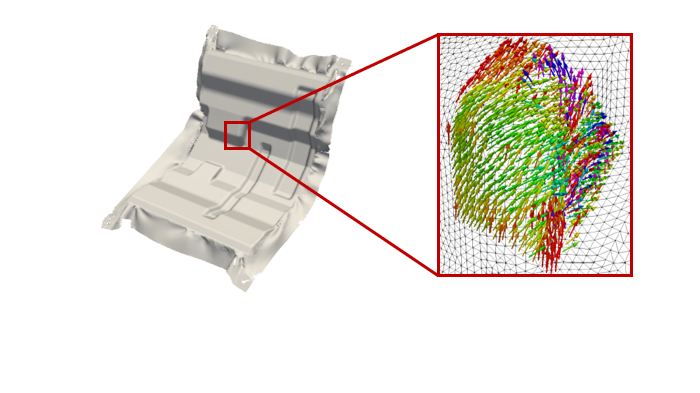
Local fiber orientation determined through a CT scan
Key information SimuDrape model
SimuDrape comes as an add-on for ABAQUS with a fully automatized pre- and postprocessing through plugins for ABAQUS/CAE, as well as advanced modeling approaches through user-subroutines for ABAQUS/Explicit.
Discretization
For the thermoforming simulation with SimuDrape, the tools as rigid surfaces since the deformations within the tools are expected to be negligible. In contrast, the eight single plies of the orthotropic laminate layup are modeled with deformable shell elements, due to their high slenderness ratio. The single plies are connected via contact constitutive equations, to accurately capture inter-ply sliding between plies.
Boundary Conditions
The processing strategy of this use case includes pneumatic gripper elements at each vertice. These gripper elements are used for the transfer from the oven to the mold, as well as for applying tensile membrane forces during forming, to improve the formability of the laminate. To accurately account for the kinematics of these gripper elements, the ABAQUS built-in translator elements are adopted to model the rotation and elongation of the gripper elements, and the tensile forces are modeled through a force boundary condition in direction of the translator elements. Besides this, gravity loading is accounting for.
Regarding thermal effects, a homogeneous initial laminate temperature of 280 °C and a constant tool temperature of 110 °C is assigned.
Material modeling
Intra-ply material modeling is based on a physically decoupled approach, to accurately model the high fiber stiffness in combination with a low bending stiffness, which is not possible with conventional shell theories. Both membrane and bending behavior are modeled by nonlinear Voigt-Kelvin approach with a temperature-dependent elasticity and a temperature- and rate-dependent viscosity. Temperature-dependency is described by a WLF-approach, whereas rate-dependency is described by a Cross-approach.
Inter-ply material modeling takes into account temperature- and rate-dependent sliding in tangential direction for both the tool-ply and the ply-ply interfaces. For the ply-ply interfaces, additionally, tacking in the normal direction is accounted for.
Thermoforming simulation results
The thermoforming simulation results obtained SimuDrape insights into formability throughout the whole forming step, from the positioning of the blank on the lower tool until the complete mold closure.
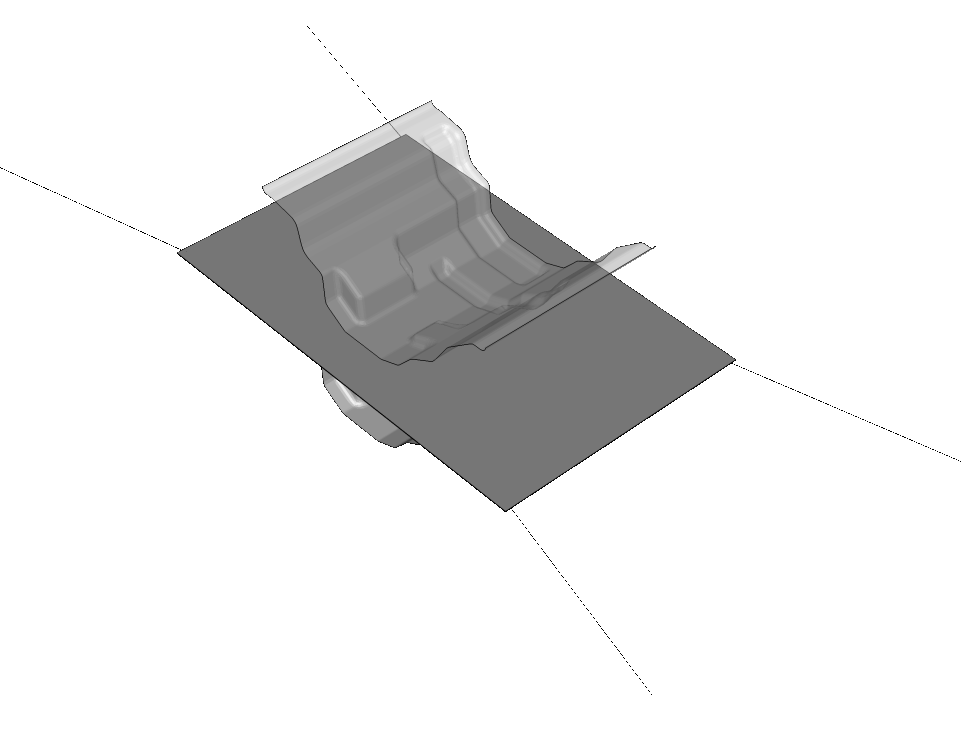
Full tool closure
The SimuDrape results are compared to surface scans of experimental tests for validation. This is done for the thermomechanical approach, as well as for the related isothermal approach under the assumption of a constant temperature of 250 °C.
The results for the fully formed part reveal a good agreement for the outer contour and material draw-in for both the thermomechanical and the isothermal approach. No major differences by assessing just the deformed surface are observed.
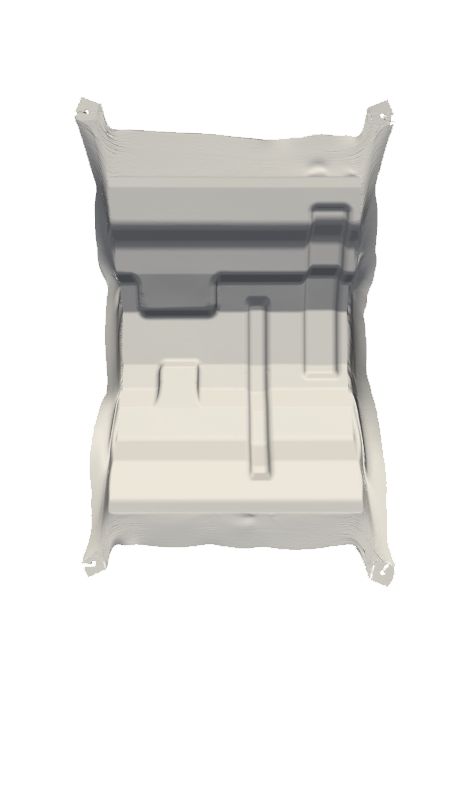
Experimental
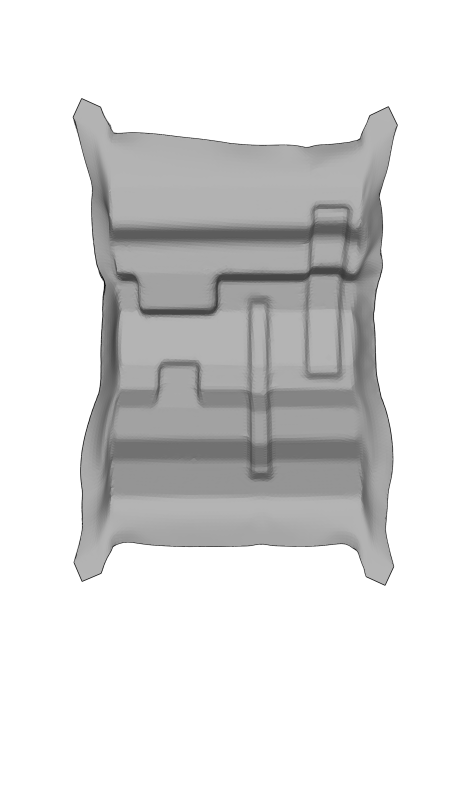
Thermomechanical
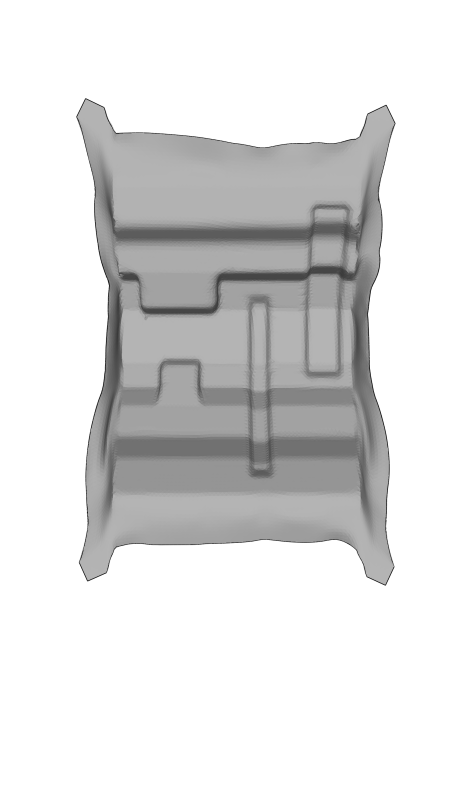
Isothermal
T = 250°C
Short shot analysis
To further investigate the prediction accuracy, a short shot analysis is conducted. For this investigation, the upper moving tool is stopped at a remaining tool travel of 5 mm. Since the blank further cools and solidifies, a partly formed part (short shot) can be ejected and the wrinkling behavior can be assessed.
The experimental result for the short shot reveals a distinct wrinkling behavior around the corner bending and at the beads. The major defect is a large fold above the bigger corner bending. For the isothermal approach, only a slight material accumulation is predicted at this location. In contrast, the wrinkling and folding are nicely predicted by the thermomechanical approach.
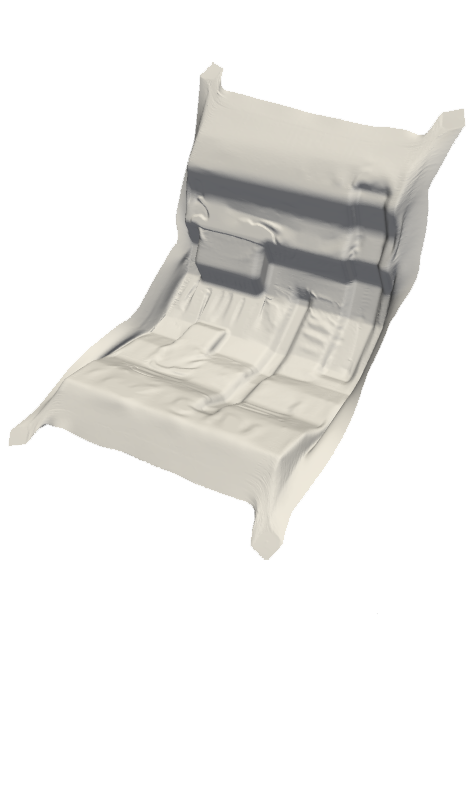
Experimental
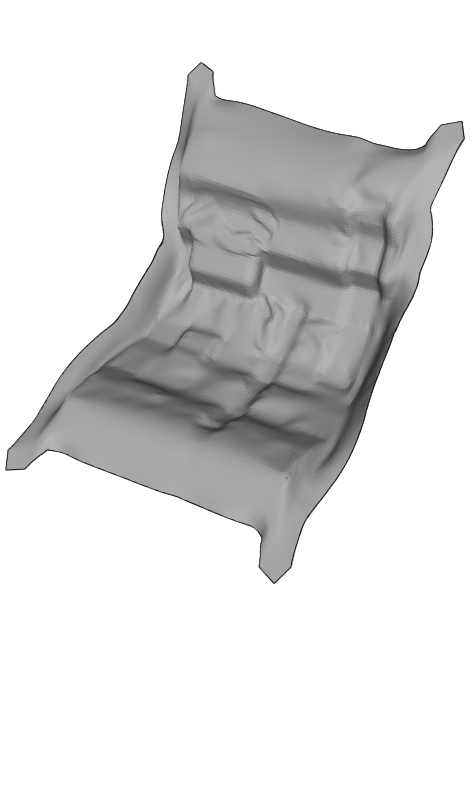
Thermomechanical
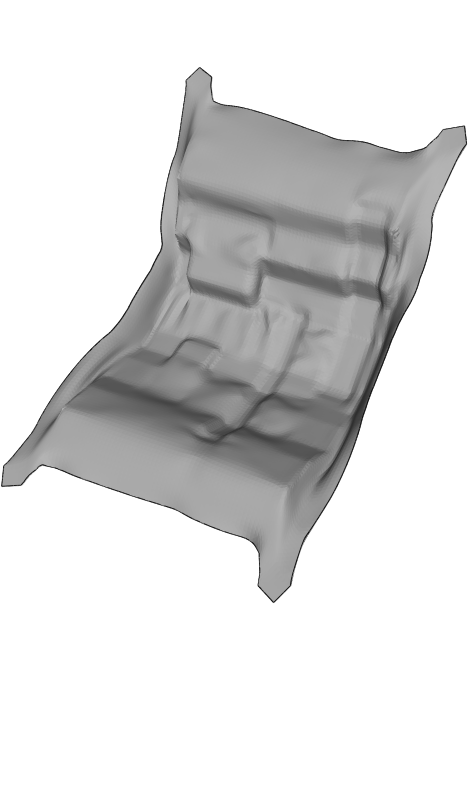
Isothermal
T = 250°C
Thermal effects
The comparison of the fully-coupled thermomechanical approach against the isothermal approach reveals the impact of considering temperature and crystallization kinetics in thermoforming simulation. During thermoforming, the blank cools due to convection and radiation at the free surfaces, as well due to the gap conductance at the tool-ply interfaces. The latter reflects the main heat sink since it renders a significant temperature gradient onto the blank.
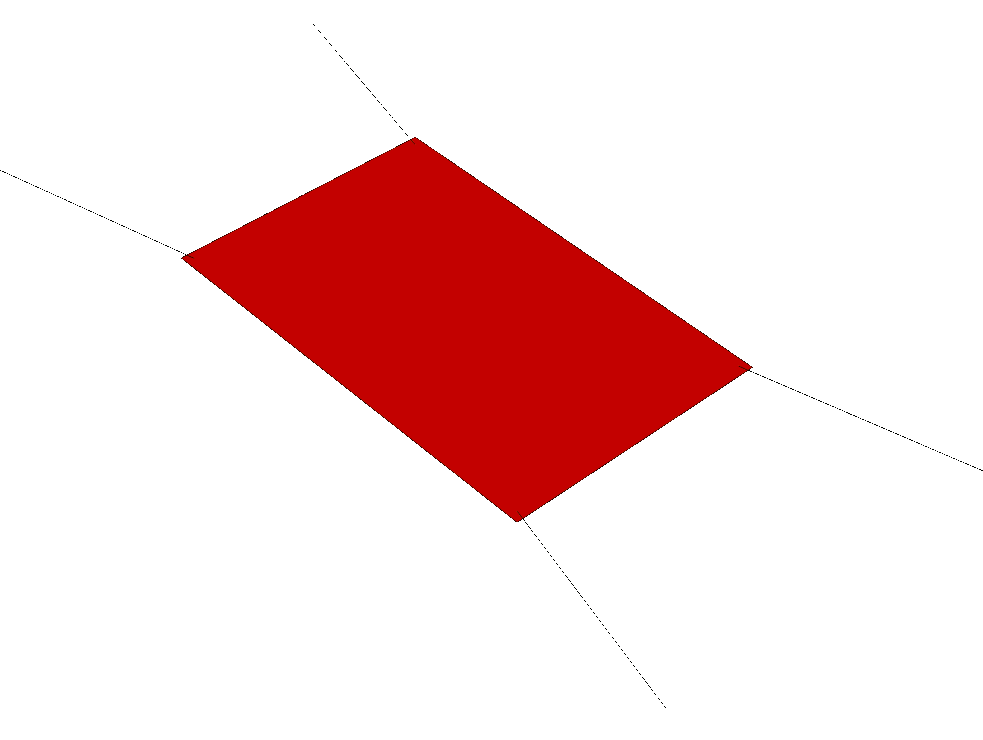
A semi-crystalline thermoplastic undergoes a phase transition during cooling, where the polymer chains are partially aligning. This phase transition is called recrystallization. SimuDrape predicts this process in terms of the state variable called relative crystallinity. Based on this, areas already solidifying during forming can be identified.
For this use case, significant cooling of the blank at the tool-ply contact areas is observed. This is especially valid for the part flanges, on which the blank is positioned at the beginning of the forming step, as well as around the corner bending to the end of the forming step. In these areas, local recrystallization is observed. Thus, the material has solidified in these areas already during forming.
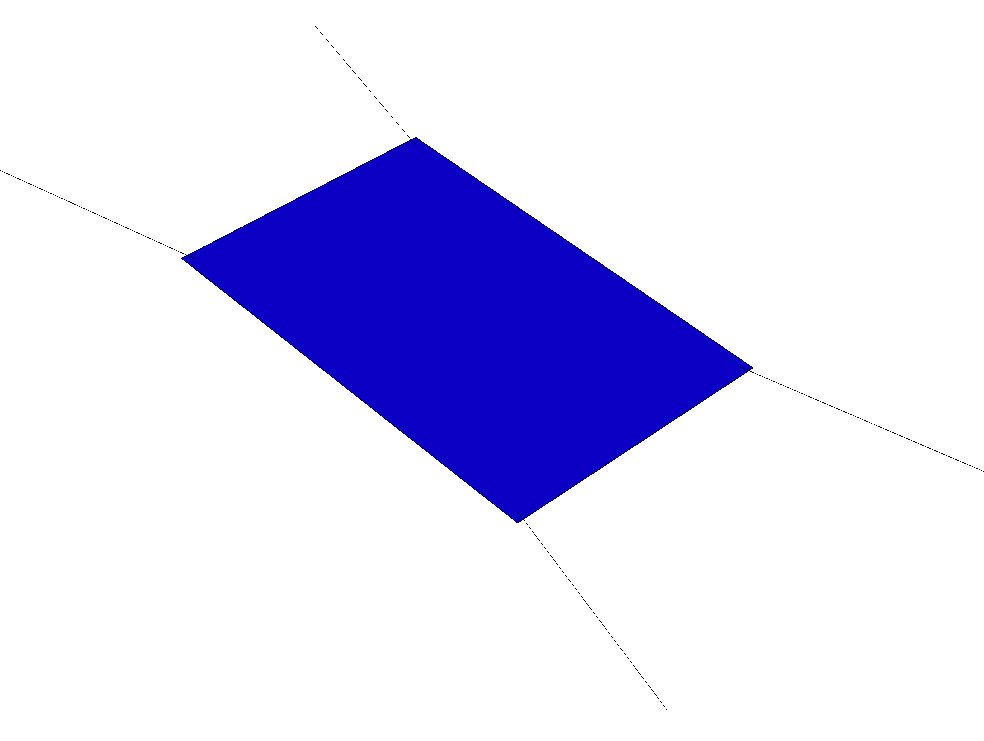
Conclusion
The validation results of this use case prove that thermoforming simulation through SimuDrape is capable to accurately predict the local wrinkling behavior and the contour after forming. Based on this, SimuDrape becomes appicable to the virtual process design in terms of several aspects. First, the manufacturability of a specific geometry can be predicted. Second, suitable manufacturing strategies and suitable processing parameters to reduce or even prevent wrinkling behavior can be determined. Third, a blank tailoring to enable near-net shaped forming can be determined.
Moreover, it is observed that the prediction accuracy for the fully-coupled thermomechanical approach supplied with SimuDrape is higher compared to the related isothermal approach. Some local defects are predicted accurately only under consideration of temperature and crystallization kinetics. Therefore, a fully-coupled thermomechanical approach for thermforming simulation is to be preferred over an isothermal approach.
References
- D. Dörr: Simulation of the thermoforming process of UD fiber-reinforced thermoplastic tape laminates. Doctoral studies. Karlsruhe Institute of Technology, Karlsruhe. Institute of Vehicle System Technology, 2019.
- D. Dörr et al.: A coupled thermomechanical approach for finite element forming simulation of continuously fiber-reinforced semi-crystalline thermoplastics. In: Composites Part A: Applied Science and Manufacturing 125, 2019.
- D. Dörr et al.: On the relevance of thermomechanics and crystallization kinetics for FE thermoforming simulation of semi-crystalline thermoplastic tapes. In: Proceeings of the 22nd international ESAFORM conference on material forming: ESAFORM 2019. Vitoria-Gasteiz, Spain, 8–10 May 2019.
Any questions?
Do not hesitate to get in contact with us if you have any questions or if you are interested in a collaboration. We are pleased if you leave us a message!